Thursday, November 20, 2014
Metronome Generator Circuit using NE555
Notes.
- The circuit can be wired on a general purpose PCB or common board.
- The circuit can be powered from a 9V PP3 battery.
- The POT R1 can be used to adjust the rhythm of the sound.
- The POT R2 can be used as volume control.
- The speaker k1 can be a n 8 Ohm tweeter.
Wednesday, November 19, 2014
Audio Peak Indicator Circuit
The main function of a series of Audio Peak indicator is to determine the occurrence of the peak level of audio signal that is more than +4 dB, equivalent to 1.25 V rms. If the received audio signal Audio Peak Indicator more than +4 dB was the LEDs in series Peak Audio This indicator will light. Audio Peak indicator circuit is mounted on the output audio system.

R1 = 10Kohm
R2 = 1.2Kohm
R3 = 220Kohm
R4-5 = 4.7Kohm
C1 = 47uF 25V
C2 = 2.2uF 25V
Q1-2 = BC550C
D1 = LED RED
Tuesday, November 18, 2014
6 Watt Audio Amplifier Schematic Circuit with TDA1519
The audio amplifier circuit is on the TDA1519 amplifier IC that is based in audio applications, which is not a aerial achievement ability can be used. The ambit TDA1519 is a ability of 2×6 watts.
The TDA1519 is an amplifier congenital Class B dual-output advance in a 9-by-line (SIL) artificial amalgamation boilerplate achievement is primarily developed for car radio applications.
Key Features of the audio amplifier IC TDA1519 are: Requires few alien components, anchored gain, acceptable bounce drive, aphasiac / standby mode, thermal protection, about-face polarity safe. Tda1519 amplifier ability rating, 14.4 volts.
Monday, November 17, 2014
Wave antenna 5 8 pro VKV FM


Friday, November 14, 2014
FM TRANSMITTER
Circuit Description
Circuit Diagram

Parts List
Thursday, November 13, 2014
BC557 based Flashing Eyes circuit with explanation
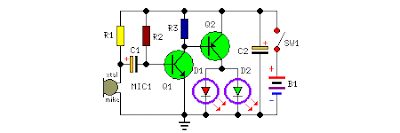
This circuit was purposely designed as a funny Halloween gadget. It should be placed to the rear of a badge or pin bearing a typical Halloween character image, e.g. a pumpkin, skull, black cat, witch, ghost etc. Two LEDs are fixed in place of the eyes of the character and will shine more or less brightly following the rhythm of the music or speech picked-up from surroundings by a small microphone. Two transistors provide the necessary amplification and drive the LEDs.
Parts:
R1 = 10K
R2 = 1M
R3 = 1K
C1 = 4.7uF-25V
C2 = 47uF-25V
D1 = 2mm LED
D2 = 2mm LED
Q1 = BC547
Q2 = BC557
B1 = 3V Battery
SW1 = SPST Switch
MIC1 = Electret Mic
Notes:
* Any general purpose, small signal transistor can be used for Q1 and Q2, but please note that R3 could require adjustment, depending on the gain of Q1. For medium gain transistors, the suggested value should do the job. High gain transistors will require a lower value for R3, i.e. about 390 – 470 Ohm. You can substitute R3 with a 1K Trimmer in order to set precisely the threshold of the circuit.
* Any LED type and color can be used, but small, 2mm diameter, high efficiency LEDs will produce a better effect.
* No limiting resistors are required for D1 and D2 even if this could seem incorrect.
* Stand-by current consumption of the circuit is about 1.5mA.
* Depending on dimensions of your badge, you can choose from a wide variety of battery types:
* 2 x 1.5 V batteries type: AA, AAA, AAAA, button clock-type, photo-camera type & others.
* 2 x 1.4 V mercury batteries, button clock-type.
Wednesday, November 12, 2014
Build Power Amplifier LM3876 Simply and Powerfull Power Amplifier
The chip on which the amplifier is based, a Type LM3876, is a member of the Overture family from National Semiconductor, All members of this family are pin-compatible and mutually interchangeable. They are typified by an internal protection (called SPIKE). In practice, the diftection ference between them is the power output. The series was described on the basis of the LM3886 in an earlier issue*.
The PCB has been designed so what it can accommodate the LM3876 (50W) as well as the LM3886 (150W). Because of this, pin5 of the IC on the board is connected to the positive supply line. This connection is not needed for the LM3876, since its pin5 is not (internally) connected (NC).
The IC is located at the side of the board to facilitate fitting it to a heat sink as shown in the photograph.
An important aspect for optimum performance is the decoupling of the unregulated supply lines by C 7-10. All earth connections go to a single terminal on the board.
Air-cored inductor L1 consists of 13 turns of 1mm dia. enamelled copper wire with an inner diameter of 10mm. The completed inductor is pushed over R7 and its terminals soldered to those of the resistor.
All electrolytic capacitors must be mounted upright. The amplifier can be muted with a single-pole switch connected to the MUTE input (pin8). This function is enabled when the switch is open. If muting is not required, solder a wire bridge across the mute terminals on the board.
Boucherot network R6-C6 is not normally required in this application, but provision has been made for it for use in other applications.
According to the manufacturers, both chips are optimalized for a load of 8 Ohm. The output power is lower when a 4 Ohm load is used or when the supply voltage is reduced. When a 4 Ohm load is used, the SPIKE protection becomes active when the supply voltage is about 27V, resulting a in a reduction of the power output to 10W. This means that it is not advisable to use loudspeaker with an impedance <8 ohm.
8>
For best result you can expand power amplifier using BPA-200 Amplifier
Part listResistor:
R1, R3 = 1 k
R2, R4, R5 = 18k
R6 = see text
R7 = 10R, 5 Watt
R8, R9 = 22k
Capacitors:
C1 = 2.2 uF
C2 = 220 uF, 160 V
C3 = 22 uF, 40 V
C4 = 47 pF
C5 = 100 uF, 40 V
C6 = see text
C7, C8 = 100 nF
C9, C10 = 1000 uF, 40 V
Inductors:
L1 = 0.7 uH - see text
Integrated circuits:
IC1 = LM3876T
Miscellaneous:
Heat sink for IC1 <1.5 k w-1
1.5>Single-pole switch - see text
Tuesday, November 11, 2014
A Hiqh Quality Headphone Amplifier Schematic
Circuit diagram:

Parts:Resistors:
P1 = 22K Potentiometer
R1 = 15K Resistor
R2 = 100K Resistor
R3 = 100K Resistor
R4 = 47K Resistor
R5 = 470R Resistor
R6 = 500R Resistor
R7 = 1K Resistor
R8 = 18K Resistor
R9 = 18K Resistor
R10 = 2.2R Resistor
R11 = 2.2R Resistor
R12 = 33R Resistor
R13 = 4.7K ResistorCapacitors:
C1 = 10uF-25V Capacitors
C2 = 10uF-25V Capacitors
C3 = 100nF-63V (PF)
C4 = 220uF-25V Capacitors
C5 = 100nF-63V (PF)
C6 = 220uF-25V CapacitorsSemiconductors:
Q1 = BC560C PNP Transistor
Q2 = BC560C PNP Transistor
Q3 = BC550C NPN Transistor
Q4 = BC550C NPN Transistor
Q5 = BC560C PNP Transistor
Q6 = BC327 PNP Transistor
Q7 = BC337 NPN TransistorMiscellaneous:
J1 = RCA Audio Input Socket
J2 = 3mm Stereo Jack Socket
B1 = 6V Battery Rechargeable
SW1=SPST Slide or Toggle Switch
Notes:
- For a Stereo version of this circuit, all parts must be doubled except P1, SW1, J2 and B1.
- Before setting quiescent current rotate the volume control P1 to the minimum, Trimmer R6 to maximum resistance and Trimmer R3 to about the middle of its travel.
- Connect a suitable headphone set or, better, a 33 Ohm 1/2W resistor to the amplifier output.
- Switch on the supply and measure the battery voltage with a Multimeter set to about 10Vdc fsd.
- Connect the Multimeter across the positive end of C4 and the negative ground.
- Rotate R3 in order to read on the Multimeter display exactly half of the battery voltage previously measured.
- Switch off the supply, disconnect the Multimeter and reconnect it, set to measure about 10mA fsd, in series to the positive supply of the amplifier.
- Switch on the supply and rotate R6 slowly until a reading of about 3mA is displayed.
- Check again the voltage at the positive end of C4 and readjust R3 if necessary.
- Wait about 15 minutes, watch if the current is varying and readjust if necessary.
- Those lucky enough to reach an oscilloscope and a 1 KHz sine wave generator can drive the amplifier to the maximum output power and adjust R3 in order to obtain a symmetrical clipping of the sine wave displayed.
Technical data:Output power (1 KHz sine wave):
- 16 Ohm: 100mW RMS
- 32 Ohm: 60mW RMS
- 64 Ohm: 35mW RMS
- 100 Ohm: 22.5mW RMS
- 300 Ohm: 8.5mW RMS
- 160mV input for 1V RMS output into 32 Ohm load (31mW)
- 200mV input for 1.27V RMS output into 32 Ohm load (50mW)
- Flat from 45Hz to 20 KHz, -1dB @ 35Hz, -2dB @ 24Hz
- 1V RMS (62mW) 0.015% 1.27V RMS (onset of clipping, 100mW) 0.04%
- 1V RMS (62mW) 0.05% 1.27V RMS (onset of clipping, 100mW) 0.1%
- Unconditionally stable on capacitive loads
Saturday, November 8, 2014
Small Audio Amplifiers Using LM386 and NE5534
During my many years building electronic things I have needed small audio amps many times, and have pretty much standardized on a few IC solutions, first and and foremost the LM386, which is small, cheap, and very easy to use. But it does not produce high quality audio... For many applications, the advantages weigh more than the distortion and noise of this chip, so that I used it anyway. In other cases I used different chips, which perform better but need more complex circuits. Often these chips were no longer available the next time I needed a small amplifier.
When I last upgraded my computer, I replaced the old and trusty Soundblaster AWE 32 by a Soundblaster Audigy. The new card is better in many regards, but while the old one had an internal audio power amplifier, the new one doesnt! Thats bad news, because I have some pretty decent speakers for the PC, which are fully passive. So, I built a little stereo amp using two LM386 chips and installed it inside the computer, fed by the 12V available internally.
But then I wasnt satisfied. The LM386 might be suitable for "communication quality" audio, which is roughly the fidelity you get over a telephone, but for music its pretty poor! The distortion was awful. So, the day came when I decided to play a little more scientifically with small audio amps, looking for a way to get good performance with simple and inexpensive means.
I set up a test bench with a sine wave oscillator running at 1 kHz, an 8 Ohm speaker, 12V power supply, and the computer with the soundcard and Fast Fourier Transform software. One channel was connected to the oscillator together with the amplifier input, the other channel to the output and speaker. With this setup I measured the harmonic content of the audio signals. I did the tests at an output level of 0.1W, which is typical for moderately loud sound from a reasonably efficient speaker. Also, I used a music signal from a CD player to test the actual sound of each amplifier.
Since I had used so many LM386s in my projects, I had several different variations. In my material box I found a slightly newer LM386N-1. So I plugged it into my test amplifier. It was even worse! The second harmonic was at -24dB, the third harmonic at -31dB, while the noise was a tad better at -84dB. Folks, thats a total harmonic distortion of almost 7%! And the 0.1W output level at which this was measured is where such a circuit is about at its best... The distortion can be plainly seen on the oscilloscope, and a visibly distorted waveform is about the most offending thing an audio designer can ever see!
Looking through my projects, I found one where I had used a GL386 chip. This is just a 386 made by another company. I unsoldered it and put it in my test amplifier. Surprise! It was dramatically better, with the second harmonic at -45dB, and the third at -57dB! The noise floor was -84dB, just like the LM386N-1. But even this level of distortion was plainly audible when listening to music. Thats roughly 0.6% THD. Some folks may consider it acceptable for music. I dont, but for communication equipment its fine. At this point, I decided to see if I could build a better amplifier, that doesnt become too complex nor expensive.
Also there were many high harmonics at roughly -84dB. That means a THD of about 0.015%. The noise floor was down at the -120dB level! The power supply rejection was excellent, with no detectable feedtrough. Playing music, this amplifier sounded really good: No audible noise, and the distortion could be heard when paying attention to it, but I doubt that the average person would detect it! Not bad, for a bias-less design!
Just to see how important the slew rate of the OpAmp is, I pulled out the NE5534 and replaced it by a humble 741, which is many times slower. The result was dramatic: The second harmonic still good at -70dB, but the third harmonic was much worse, at -48dB. Also there were many high harmonics at the same -48dB level. Given that second harmonic distortion doesnt sound bad to most people, but third harmonic does, and high harmonics are even worse, it came as no surprise that the amplifier with the 741 sounded bad.
At low volume it sounded particularly bad! So I returned to the oscillator and measurement setup, testing at lower output power, and found that while the second and third harmonics followed the output, the high harmonics stayed mostly constant! So, at very low output, the high harmonics became very strong relative to the output. All this is the effect of the slower slew rate of the 741, which makes it less effective correcting the crossover distortion of the unbiased transistors. Interestingly, the noise floor of the 741 circuit wasnt bad: -118dB.
Just for fun, I tried this circuit with a third OpAmp: The TL071, which is good, but not as good as the 5534. The results: Second harmonic at -72dB, third and the high ones at -60dB, and the noise at -120dB. Its interesting that the second harmonic is much more suppressed than the third one. That must be a balancing effect of the symmetric output stage, and the better symmetry in the TL071 compared to other OpAmps.
Its worthwhile to note that this amplifier can be simplified a lot by using a split power supply. R1, R2, C1, C2 and C4 would be eliminated! But then you need the capacitor removed from C4 to bypass the negative supply line. The positive input of the chip goes to ground, while pin 4 and the collector of Q2 go to the negative supply. The rest stays the same. If you use a +-15V supply, the available RMS output power grows to over 10 Watt! Of course, you then need larger transistors. And since larger transistors are slower, the distortion will rise somewhat. An added benefit of a split supply is that the popping noise when switching on and off is eliminated.
The third harmonic was at -84dB, and the best improvement was that the higher harmonics had simply disappeared! They were all below the noise floor, which stayed at -120dB. Actually, this noise floor seems to come from the soundcard A/D converter, so that the actual noise of this and the above amplifier may even be better! With music, this amplifier sounded perfect - clean and smooth. And Im pretty confident that the THD is well below the limits of my measurement setup, which is 0.01%.
The quiescent current was around 10mA. When lowering it to about 3mA, the high harmonics started to rise out of the noise floor. If you want to adjust the bias for the exact best quiescent current, there is a simple trick: Lift R4 from the output, and connect it to pin 6. Now the output stage has been left outside the feedback loop, and all its distortion will show up at the output. Watching the signal on an oscilloscope, or even better on a real time spectrum analyzer (soundcard and software), adjust the trimpot to the lowest distortion level.
Have a current meter in the supply line and make sure that you dont exceed 30mA or so of quiescent current, in order to keep the small transistors cool. But most likely the best distortion will be at a current lower than that. Once the adjustment is complete, return R4 to its normal position. Now the full gain and slew rate of the operational amplifier is used to correct the small remaining cross-over distortion of the output stage, and the distortion will certainly disappear from the scope screen, from your ears, and possibly fall below the detection level of the spectrum analyzer!
This circuit can also be run from a split power supply, by exactly the same mods as for the previous circuit. And since the transistors are properly biased, there isnt any significant distortion increase when using larger transistors. Be sure to use some that have enough gain - you have only a few mA of driving available, and with a +-15V power supply and an 8 Ohm speaker, there can be almost 2A of output current! So, you need a gain of 300 at least. There are power transistors in the 4A class that provide such gain, and these are good candidates. The other option is using Darlington transistors, which far exceed the gain needed here. But they will again increase the distortion, not very much, but perhaps enough to make it audible again.
Thursday, November 6, 2014
Power Supply Failure Alarm
Wednesday, November 5, 2014
Battery Saver
For the actual switch we’re using a well-known MOSFET, the BS170. A MOSFET (T2 in the circuit) used in this configuration doesn’t need a current to make it conduct (just a voltage), which makes the circuit very efficient. When the battery is connected to the battery saver circuit for the first time, capacitor C2 provides the gate of the MOSFET with a positive voltage, which causes T2 to conduct and hence connect the load (on the 9 V output) to the battery (BT1). C2 is slowly charged up via R3 (i.e. the voltage across C2 increases).
You only need to hold down the switch for a few hundredths of a second to fully discharge C2. In our prototype, connected between a 9 V battery and a load that drew about 5 mA, the output voltage started to drop after about 26 minutes. After 30 minutes the voltage had dropped to 2.4 V. You should use a good quality capacitor for C2 (one that has a very low leakage current), otherwise you could have to wait a very long time before the switch turns off!
This stops T2 from conducting and the load is turned off. The choice of value for R2 determines how dark it has to be before T1 starts to conduct. The battery saver circuit can be added to devices that use 6 or 9 volt batteries and which don’t draw more than 100 mA. The circuit can be built on a piece of experimenter’s board and should be made as compact as possible so that it can be built into the battery powered device.
Tuesday, November 4, 2014
Car Reversing Horn with Flasher
Fig. 1: Car reverse horn Circuit Diagram:
When the junction of diodes D1 and D2 is low, the astable multivibrator is disabled to stop oscillating. The output of the astable multivibrator is fed to the speaker through capacitor C6. The speaker, in turn, does not produce sound.
Assemble the circuit on a general-purpose PCB and enclose in a suitable cabinet. Connect the circuit to the car reverse switch through two wires such that S1 shorts when the car gear is reversed and is open otherwise. To power the circuit, use the car battery.
The flasher circuit (shown in Fig. 2) is built around timer NE555, which is wired as an astable multivibrator that outputs square wave at its pin 3. A 10W auto bulb is used for flasher. The flashing rate of the bulb is decided by preset VR1.
Monday, November 3, 2014
20 WATT FLUORO INVERTER used tip3055
The transformer is wound on a ferrite rod 10mm dia and 8cm long.

Do not remove the tube when the circuit is operating as the spikes produced by the transformer will damage the transistor.
The circuit will take approx 1.5amp on 12v, making it more efficient than running the tubes from the mains. A normal fluoro takes 20 watts for the tube and about 15 watts for the ballast.
Sunday, November 2, 2014
AUTOMATIC AIRFLOW DETECTOR ELECTRONIC DIAGRAM
Sensor used in this circuit is a bulb filament. If there is no airflow, the filament resistance would give low value. On the other hand, if there is airflow, the filament resistance would varies. The variation of the resistance is caused by the heat difference between filament. It also effects to the voltage variation passing through that filament. That voltage difference will be processed by LM339 op-amp and displayed by the LED.
Parts list :
- LED1 : LED 5mm
- IC1 volt regulator : LM7805
- Polar Capacitor C1 : 47 uF/15V
- Resistor R1 : 100 ohm
- Resistor R2 : 470 ohm
- Resistor R3 : 10k ohm
- Potensiometer R4 : 100k ohm
- Resistor R5 : 1k ohm
- IC2 op-amp : LM339
- Bulb filament
- Power supply/battery 12V